This document is intended as a summary of the research and experimentation I have done to gain information about the processes of annealing brass. All the information here can be backed up with data from my experiments or the published accounts of experiments by others. It is a living document and will be updated as new information comes to light.
This version current as of 2021/11/26
The problem of material cracking in storage was encountered by many brass working businesses very early in the 20th century, particularly in the plumbing, refrigeration and munitions industries. The problem was serious, so public and private industries teamed up with researchers and did much research into the issue. Within about 15 years they had a diagnosis: stress-corrosion cracking (SCC), sometimes called season cracking, a corrosion mechanism wherein the presence of tensile stresses made the deterioration much faster and more serious than either stress or corrosion would do alone. They also came up with a solution: annealing. A low temperature heat treatment that reduced or eliminated the stresses built up in the material by severe forming operations was sufficient to make SCC essentially a thing of the past, at least so far as they were concerned.

Despite the thoroughly researched nature of SCC, shooters and reloaders somehow avoided the belief it might apply to them, and by the 1950s when questions about neck cracking arose in the pages of popular gun magazines the technical editors there had their own theory, namely embrittlement by cold work. They stated that deformation of the case during firing and resizing would make the case necks brittle, but that annealing would soften and recrystallize the brass, essentially resetting the mechanism back to zero and allowing several more reloads before the problem cropped up again. If a shred of evidence or supporting data was ever presented to support this theory, I have not found it.

To test the cold work theory, I built a mobile loading bench onto the tailgate of my truck, and went to the range. Ten .223 cases were loaded and fired repeatedly in the course of an afternoon, until all had failed. The average case life was over 20 firings, and the last one lasted until the 29th firing. A case that had been fired 27 times was subjected to a reverse-bending ductility test and passed. The case that had lasted through 29 firings was sent to a lab and tested for hardness and examined metallographically. Hardness was not especially high for cold-worked brass, and the failure zone exhibited characteristics typical of a ductile fracture. It was concluded that for cold work to make a case brittle it would require several dozens of firings, if it is possible at all.
At the same time, some cases that had split during normal use in my rifles were also subjected to some materials testing. They passed the reverse-bending ductility test. They exhibited only moderate hardness, considerably less than the 29-times fired case. The metallography though, was very different. This time, the failure characteristics were consistent with SCC.
With this in mind, I contrived another test. An environmental test chamber was built to expose cases to ammonia, the chemical most commonly known to cause SCC in brass. A batch of .223 Remington cases that had been loaded and fired a variety of times was loaded into the test chamber with the following result:

With it demonstrated that reloading cases does not make them brittle with any reasonable use but does quickly make them susceptible to SCC, the next step was to figure out how to solve the problem. But of course it didn’t take much figuring, as ammunition producers around the world solved it a century ago. The solution to case cracking is to relieve internal stresses by annealing the necks of your cases.
To demonstrate the effect of annealing, a variety of annealing temperatures were employed for five seconds on brass that had been fired and reloaded either once or three times. The cases were then subjected to a refined version of the SCC susceptibility test, and samples were taken for lab characterization of the material.
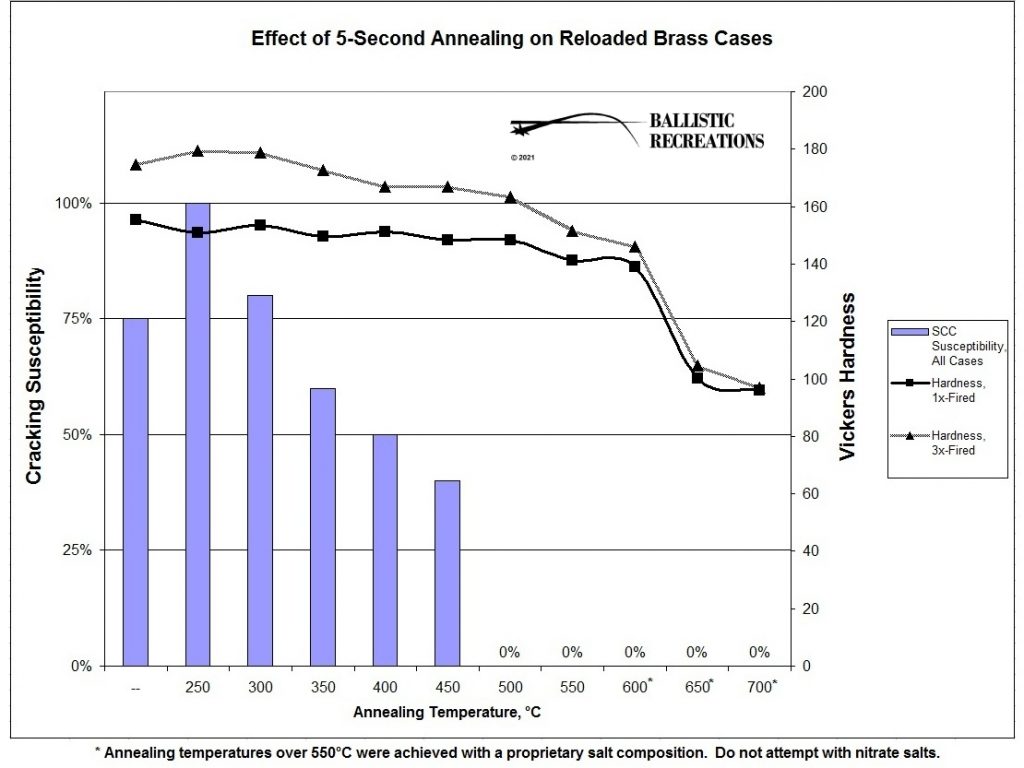
Results showed that a large fraction of cases that had been loaded and fired even once were susceptible to cracking, and annealing at very low temperatures like 250°C made the problem worse, not better. However, annealing at temperatures of 500° or greater solved the problem completely.
A result that will probably surprise many is that cracking was not related to hardness. Cracking rates went from 100% to 0% with no significant change in hardness of the material. There was also no change in material microstructure that could be discerned by optical microscope. The benefit is derived entirely from stress relief. Softening the material is possible, but it requires a recrystallization anneal, with temperatures over 600°C and inevitable grain growth. Studies have shown that hardness increases rapidly with first use of a case, but typically levels out after a few firings at a little under 200 HV. There does not appear to be any harm in leaving it at this level, and softening it significantly will alter the grain structure of the brass case.
It is thus concluded that annealing for five seconds at 500°-550°C effectively mitigates cracking while not altering the factory microstructure, and this is the practice I recommend for most calibers (the subject cases were .223 Remington, the results are expected to be the same for any that have similar neck thickness).
For more details on the experiments that yielded the above findings, readers are encouraged to look at the full written reports of my experiments, in the Annealing Knowledge Centre section of my webpage at www.ballisticrecreations.ca.