G. Chambers, Ballistic Recreations
Introduction
Although the metallurgy of brass has been extensively studied and understanding is quite advanced at the academic and industrial levels, technical knowledge among reloaders has typically been poor. There are many misconceptions among shooters as to the precise nature of the brass material they work with, what effects they can achieve, and what constitutes best practices to get there. There is a false belief, for example, that routine cold work associated with loading and firing will make brass brittle, eventually resulting in fracture when the case is fired. In reality, cracks with a brittle appearance in brass cartridge cases are almost always caused by a mechanism known as stress-corrosion cracking (SCC).
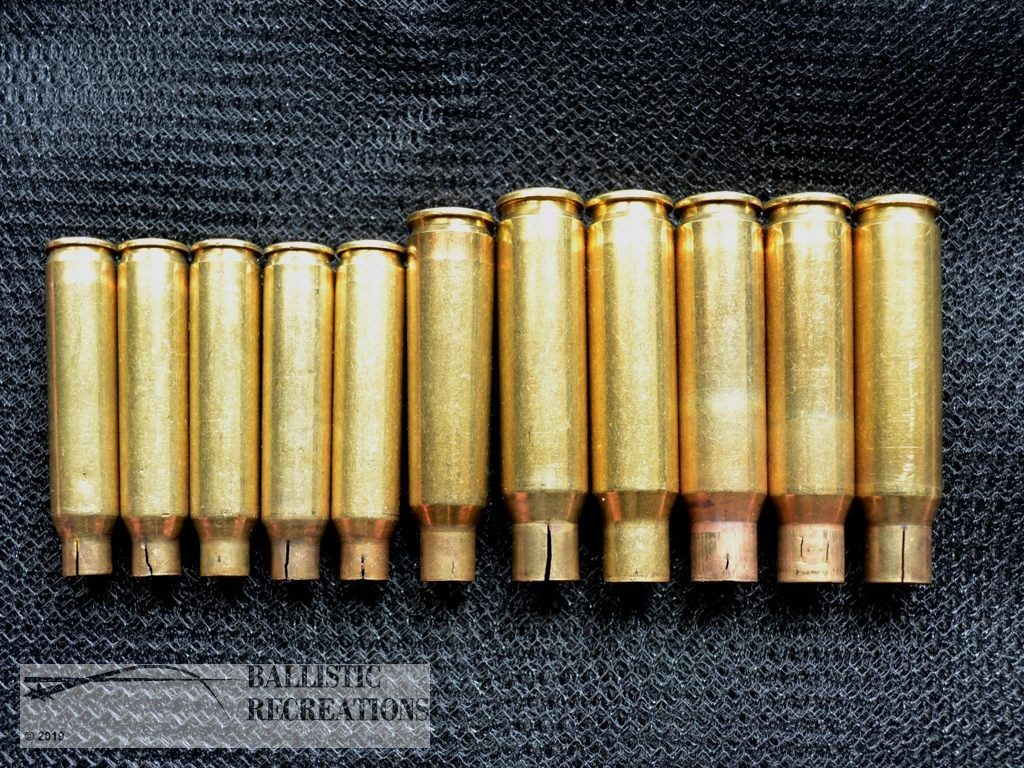
Annealing treatments are performed on brass cases several times throughout the manufacturing process, but most of these treatments are tied to the deep drawing processes used to turn brass strip into formed cases and are of only academic interest to the user of the case. The exception is the final annealing of the neck and shoulder of bottlenecked cases that is done to reduce susceptibility of the case to cracking in storage by SCC. Just as the factory drawing and forming operations will induce stresses that make the cases vulnerable to cracking, the reloader’s repeated firing and resizing of a case will reintroduce stresses to the neck area and again make the case susceptible to SCC. It is therefore not surprising that reloaders have long adopted neck annealing techniques into their operations, with adjustments suitable to the scale and economy of their loading operations.
Unfortunately the adoption of effective annealing practices has been hampered by the lack of knowledge, including knowledge as essential as what temperatures could be used when annealing. Most early writers simply recommend torch heating until a dull red is achieved. The earliest mention I can find thus far of a specific temperature is in a magazine column from 1962, wherein author William Dresser states that he uses a 700°F (371°C) welder’s temperature crayon to control annealing1. Later, John Wootters identified the annealing range as 750°-950°F (399°-510°C)2. In the internet era, online opinion seems to have largely settled on 750°F as the ideal target temperature, though supporters of both lower and higher numbers can be readily found.
As temperature is by far the most critical variable in any heat treating operation, the necessity of understanding the impacts of changing temperature when annealing are obvious. This test was thus conceived to supply some answers that have been wanting for several decades. The primary test will be the impact of annealing on case susceptibility to neck cracking by SCC, with some secondary evaluations of hardness and grain structure.
Test Procedure
Brass cases for this test were acquired as factory-loaded ammunition in .223 Remington calibre, taken from a retail package of 200 cartridges (Remington Arms Co. Mega-Pack, product code L223R3A, lot# B21FAI). No chemistry check was performed on the cases, and it is assumed that the material corresponds to UNS C26000 cartridge brass (nominally 70Cu-30Zn), as is commonly used for small arms ammunition cases worldwide. The study began with firing the factory cartridges in an AR-15 rifle built with a standard Colt M16A1 barrel.
One group of cases was tumbled clean in plain crushed walnut shells, resized and deprimed, annealed (see below for annealing details), then assembled as dummy rounds with a 55-grain FMJ bullet and reinstallation of a fired primer. These are referred to as the 1x-fired case group.
To create a second group of cases a mobile loading bench was set up at the firing range. Factory cartridges were fired in the same AR-15 rifle mentioned previously then immediately reloaded. The process was repeated without any cleaning operations until the cases had been fired a third time, then they were taken home and tumbled clean in walnut shells. The cases were finally loaded as dummy rounds as above. This group is referred to as the 3x-fired case group.
Sizing and bullet seating were conducted using a standard, full-length die set from Lee Precision.
Annealing was carried out in temperature-controlled molten salt baths. Because molten salts have limited windows of safe and effective operation, two salt bath systems were used to cover the full range desired. Bath temperature was controlled by a REX C-100 PID controller for both systems. A blend of nitrate salts sold by Ballistic Recreations was used for temperatures up to and including 550°C, in conjunction with a Lee Precision Melter pot with the factory thermostat disabled. For temperatures of 600° or greater, a proprietary high-temperature salt blend was used, along with a custom made salt pot heated by an electrical resistance element. Though the latter salt is reasonably effective for study purposes, it has some rather inconvenient properties that make it unsafe and impractical for routine annealing. It’s also rather expensive. As such it is not offered for sale.
Each case was annealed by immersing it mouth down in an annealing fixture for five seconds, with insertion and removal by hand and using a running stopwatch as a timing guide. The bath depth was sufficient to immerse the complete neck, shoulder, and a small fraction of the case body. Following immersion each case was quickly tapped on the fixture top plate to knock out as much salt as possible then immediately dropped into a pail of ambient temperature water. After removal from the quench water cases were flushed with clean tap water to ensure all salt was removed.
An environmental chamber was constructed to enable controlled exposure of the dummy cartridges to an environment likely to promote SCC. The chamber comprised a plastic 20-litre bucket with a platform placed about 170mm above the floor of the bucket. The platform featured five elongated slots, each about 140mm long x 15mm wide. Specimen dummy cartridges were fixed into holder strips that held five each, and the strips were then placed on the platform so that the cartridges hung inverted through the slots. One strip was placed over each slot, so that 25 cartridges could be tested at one time. An effort was made to stagger the specimen order on each holder to offset any effect of position within the chamber. A solution of ammonium hydroxide was poured into the bottom of the bucket, comprising 2ml of household ammonia + 13ml tap water. Based on density the household ammonia was estimated to be 16% NH3 by mass.
The air space over the platform was packed with plastic bubble wrap, and a gasketed lid fitted to the bucket to ensure a tight seal. The test chamber was nested into a second 20-litre bucket, this one partially filled with water and with a 100W, thermostatically-controlled immersion heater in the bottom. The assembly was wrapped in multiple towels as insulation, the heater powered on, and the test allowed to proceed undisturbed for approximately 120 hours (five days). Upon completion of each test the outer bath water was checked for temperature and was found to be between 35°C and 37°C each time.
In most instances, five cartridges were SCC tested for each firing group / annealing temperature combination. However to accelerate the testing schedule only three specimens that had been annealed at 650°C or 700°C were tested. Additionally two dummies that had not been annealed were included in each test run.
Following the test the chamber was opened and each specimen holder removed and rinsed in tap water, then dried. A quick visual inspection was done for each holder, then specimens were checked for cracks using a red-on-white contrast dye penetrant inspection method without removing them from the holders.

Selected cartridges were disassembled with a kinetic bullet puller and the neck and shoulder portions cut from the cases and mounted in epoxy in preparation for metallographic evaluation and microhardness testing.
Test Results
Four test runs were required to accommodate all specimens, and all runs were completed without significant problem or interruption. At test completion cartridges typically showed clear effects of the corrosive environment, with dulled surfaces, black staining, and light green corrosion products commonly evident. Only a single crack on one specimen was noted by visual inspection, however dye penetrant testing highlighted almost 200 cracks spread over 38 specimens.


As a casual observation, cracking seemed to be most severe in terms of length and number of cracks in specimens that had been annealed at the lowest temperatures (250°, 300°, and 350°), even more so than in samples that were not annealed at all. To keep the analysis simple however, cases were simply noted as having developed cracks, or not. The results are presented in the following table:

Transverse sections midway along the case neck were prepared for one sample of each firing group / annealing temperature combination. A case that was disassembled from an unfired factory cartridge was prepared similarly for comparison. Hardness values were measured using the Vickers hardness method (0.2kg load), with results taken at four points around the section and averaged to produce the following results:

After hardness testing, each sample was polished to a fine surface and etched with ammonium hydroxide + hydrogen peroxide solution to reveal the microstructure. During this stage it was discovered that one sample, from the 1x-Fired group and annealed at 350°, exhibited several cracks extending from the inside surface, both partial wall and through wall. This sample did not have any cracks detected by dye penetrant.

Microstructure in the neck of the unfired case was typical of what I seen in other brands and calibers of new, bottlenecked rifle cases, comprising very finely textured cold-worked material with a minor fraction of recrystallized grains. Assessment of such fine structures is typically considered beyond the capabilities of optical microscopy, but I attempted a simplistic evaluation by photographing what I judged a typical view of the structure, then measuring the largest dimension of the largest discrete feature that I could resolve. A similar assessment was done for each sectioned specimen.


Microstructures of the 1x-fired group were virtually indistinguishable from factory new until annealing temperatures attained 650°. At that temperature a number of relatively large, irregularly-shaped new grains became apparent. The new grains occupied an estimated 30% of the material volume, with the remainder maintaining the fine-textured, cold-worked structure seen previously. The specimen annealed at 700° was similar: new grains were about the same in number, but larger so that they occupied an estimated 50% of the material volume.
Microstructures of the 3x-fired group annealed at low temperatures were again indistinguishable from that of the factory new case. With a 550° anneal, limited number of grains near the OD surface demonstrated some growth. A considerable number of new and slightly larger grains were visible in the 600° annealed sample. Like with the 1x-Fired group, at 650° and 700° the samples exhibited a majority fraction of new and sizeable grains in a matrix of finely-textured, cold-worked material, but the 3x-fired group had a finer grain size. At 700° the volume of recrystallized material was estimated at 70%.
Discussion
The original, and still best understood, intent of case neck annealing is to prevent cracking of the material by the mechanism of stress-corrosion cracking. This fact has unfortunately been largely overlooked in the field of handloading, thanks to a decades-long repetition by credible sources of the theory that cracks are due to cold work in the firing and reloading process making brass brittle. In reality, a close examination of any bottlenecked rifle case that has developed neck cracks in fewer than 20 firings most commonly points to SCC. Thus the practice of annealing to prevent SCC is extremely relevant to the handloader. With that in mind, some valuable information can be found in the results of this test.
SCC is a synergistic mechanism, where the interaction of stress and corrosive environment does far more damage than stress and corrosion would be expected to do on their own. As the reloader may find corrosive environments to be unpredictable and often unavoidable, it is best managed by ensuring that stress levels are below the threshold necessary to promote cracking. For that reason I employed a very aggressive corrosive environment that could be expected to cause cracking wherever sufficiently high stresses were present. The first important conclusion then to draw from the testing is that 50% of cases were sufficiently stressed as to experience cracking after just one cycle of fire and reload. This is a confirmation of an earlier experiment I did starting with virgin, unprimed Hornady .223 cases, which showed cracks appearing in cartridges that had been loaded and fired only once. With threshold cracking stresses so easily attained the need for annealing is apparent.
After studying the data, I found that the best way to present the results was the simplest: I combined both firing groups together to give a single cracking rate versus annealing temperature, as so:

This presentation makes clear that reloaded brass cases have a high susceptibility to cracking by SCC, and cracking susceptibility actually rises if annealing is conducted at a low temperature. Annealing at the 750°F (399°C) number so often cited in brass annealing discussions is within a range that significantly lowers that susceptibility, however cracking remains a distinct possibility unless the case is annealed at 500°C or more, at which point cracking drops to zero. This does represent an upwards shift compared to my first round of cracking tests done in 2019. That test found that cases annealed at 450° could be expected to be crack-free, but the sample size was much smaller and the test procedure less developed than the current work.
The finding that cracking susceptibility actually rises with low-temperature annealing was a corroboration of the informal observation that cracks seemed longer and more numerous in those samples. It’s also interesting when viewed in conjunction with data presented in many studies that cartridge brass hardness rises slightly when annealing is conducted at temperatures around 250°C, a topic that interested the Australian Department of Defense enough to investigate if it affected SCC susceptibility in 7.62x51mm cases3. In contrast to this work, they did not find any such association.
Secondary evaluations revealed that neither hardness nor microstructure underwent much change in the interval between very high cracking susceptibility and zero cracking susceptibility. This is a strong indicator that cracking susceptibility is related to stress rather than any strength or microstructural characteristic.

Many shooters believe that annealing is expected to reduce hardness imparted by cold work, this work challenges that belief. Hardness increases readily when a case is loaded and fired, while softening due to annealing requires much more energy to achieve. There is a wide range of annealing temperatures that reduce cracking potential while having no major effect on hardness. Softening does eventually become significant at temperatures over 600°, but is accompanied by substantial recrystallization and grain growth, resulting in an altering of the factory microstructure. As previously stated, the factory microstructure is probably managed soley with manufacture in mind. The demands associated with reusing a case are very different from the demands associated with manufacturing it, and it is not at all clear to me what consequences, if any, may arise from altering that microstructure.
As much as cracking mitigation is the best understood result of case neck annealing, in recent years there have been claims that annealing can impact other aspects of ammunition loading. In particular some accuracy claims have been made, though for the most part any data supporting the claims or attempt to explain a mechanism for such an improvement have been notably absent. An exception is work published by Findlay that collected data on over 120 five-shot groups fired by four shooters over a period of six weeks, finding that vertical dispersion could be reduced by up to 50% when annealed cases were compared to non-annealed cases4. It should be noted that this result was observed with competitive shooters firing match-grade components in custom rifles, and the reduction was less than 0.3 MOA in all instances.
The mechanism proposed by Findlay is improved dimensional uniformity of reused cases, with a specific strategy of annealing necks and shoulders to a hardness of 95-100HV after every firing to minimize the material’s elastic response. Adherents of this theory may find the results of the current study useful, as it suggests 650°-700°C as a target annealing range. This is not a practical number with current molten salt compositions, but should be achievable with flame processes. The reader is reminded that my data is incomplete, as it studied only a single anneal. What may happen as a case is used and annealed many times is unclear but it is certain that a 700° anneal puts the material into a transition range with regards to hardness and microstructure, which may make outcomes unpredictable. It is also clear that it is well beyond the temperature range used by the factories that manufacture the brass, who generally gravitate to the stable, fine-grained structure realized at lower annealing temperatures.
Conclusions
Neck annealing to prevent stress-corrosion cracking is an important procedure for the reloader wishing to get long life from his brass cartridge cases. This study makes several findings that may help guide reloaders in their development of a process for use at home.
Major findings include:
– An earlier finding that brass cases may become susceptible to neck cracking by SCC after a single cycle of loading and firing is reinforced.
– Annealing at temperatures from 350°- 450°C (roughly 650°- 850°F) for five seconds results in a perceptible reduction in cracking potential, but a substantial risk remains.
– Annealing at temperatures of 500°C (932°C) or higher results in instances of cracking dropping to zero.
– Annealing temperatures up to 550°C produce no microstructural changes in the brass material that can be resolved by optical techniques.
– Given the above, it follows that a shooter who regularly neck anneals cases in the range of 500°-550°C for five seconds can expect complete mitigation of cracking without affecting the fine-grained factory microstructure of the brass.
– Annealing temperatures of 600°C and greater begin to produce substantial metallurgical changes in the material, simultaneously resulting in reduced hardness, increased recrystallization, and grain growth of the material.
– Susceptibility to stress-corrosion cracking has little or no relationship to brass hardness. A case fired once and annealed at 250°C had the same hardness as one fired three times and annealed at 550°C, yet one had a very high susceptibility to SCC and the other had none. Cracking tendencies appear to be driven mostly or entirely by the stress levels on the material.
GBC 2021/11/23
References
1- The American Rifleman, September 1962, p.42
2- John Wootters, The Complete Handloader, Outdoor Life Books (1988)
3- D. Saunders, The Low Temperature Annealing of 7.62mm Brass Cartridge Cases: Stress Corrosion Susceptibility, Australia Department of Defense (1980)
4- A. Findlay & M. Findlay, Annealing Under the Microscope Part 5 Sec. 2, retrieved online from https://www.ampannealing.com/articles/57/annealing-under-the-microscope/, published 2019, retrieved 2020/03/31